Electric flange ball valve installation instructions
The working principle of the electric flange ball valve is to open and close the valve through the power drive and rotate the valve stem. It has the characteristics of light switch, small size, reliable sealing, simple structure and convenient maintenance. Due to the sealing surface and spherical surface of the electric flange ball valve Often in the closed state, it is not easy to be eroded by the medium, and it is widely used in various industries. As for the correct installation of the electric ball valve is related to the operating conditions of the working conditions and the safety during use, the user should understand the instructions for use.
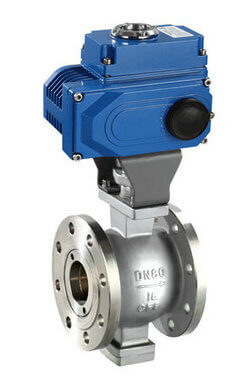
electric V type ball valve
1. Preparation before installation
1. The front and back pipelines of the electric flange ball valve have been prepared. The front and rear pipes should be coaxial, and the sealing surfaces of the two flanges should be parallel. The pipeline should be able to bear the weight of the ball valve, otherwise the pipeline must be equipped with proper support.
2. Purge the pipelines before and after the valve to remove the oil, welding slag and all other impurities in the pipe belt.
3. Check the mark of the ball valve to find out that the ball valve is intact. Fully open and close the valve several times to verify that it is working properly.
2. Installation method and steps of electric flange ball valve
1. Remove the protective covers on both sides of the flange, and rinse and clean with the valve fully opened.
2. Check the valve hole, and then clean the valve hole. Flush and remove all accumulated impurities in the pipeline (these substances may damage the valve seat and ball).
3. During installation, please do not use the valve stem or handle (handwheel) part of the valve as a fulcrum for lifting objects to avoid collapse and other accidents.
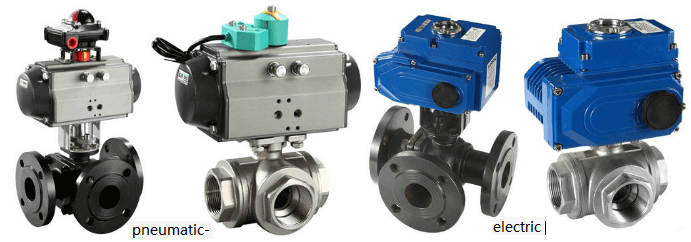
pneumatic-electric-three way ball valve-flange-crew-T-L-type
4. Install the valve on the pipeline. This type of valve can be placed in any position and direction of the pipeline. The two ends are each fixed on a flange piece, and then flange gaskets are added between the two flange plates to fix it.
5. The pipeline near the installation point should not be drooping or bear external forces. Pipe supports or supports can be used to remove the deviation of the pipeline.
6. Finally, use bolts to align the two flange pieces with the flange holes and tighten them to make them tightly connected. (Some pipes or pipe fittings have their own flanges.)
3. Operation and use of electric flange ball valve
1. Make sure that the pipelines and valves have been flushed before operation.
2. The operation of the valve is completed by rotating the valve stem (manual or automatic control mode): when it rotates 1/4 turn (90°) clockwise, the valve is closed. When the reverse rotation is 1/4 turn (90°), the valve opens.
3. When the direction of the handle or the groove on the top of the valve stem is parallel to the pipeline, the valve is open.
4. The torsion of the valve stem will vary according to the following factors: the length of time the valve is opened and closed, the medium of the pipeline system, the pipeline pressure and the type of valve seat, etc.
Related Products: Pneumatic Flanged Ball Valve
TH Valve is a professional manufacturer of butterfly valve, gate valve, check valve, globe valve, knife gate valve, ball valve with API, JIS, DIN standard, used in Oil, Gas, Marine industry, Water supply and drainage, fire fighting, shipbuilding, water treatment and other systems, with Nominal Diameter of DN50 to DN1200, NBR/EPDM/VITON, Certificates & Approvals: DNV-GL, Lloyds, DNV, BV, API, ABS, CCS. Standards: EN 593, API609, API6D