Description and classification of valve connection
Classification and description of valve connection methods: Nowadays, the application range of valves is wider and
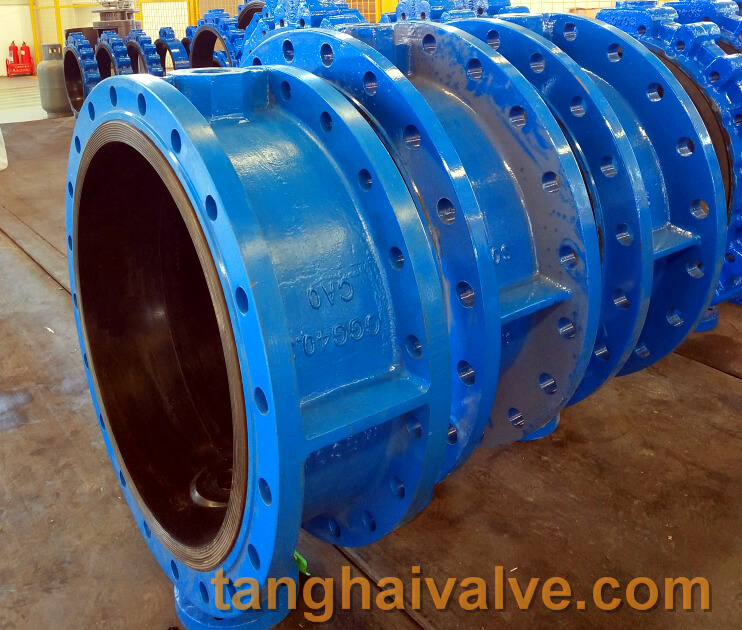
double flange butterfly valve body
wider, and corresponding valves should be used in different environments. The connection between the entire valve and the pipeline or equipment is different. Regardless of installation, use and maintenance, attention should be paid to the improper connection of the valve, which may cause the valve to run, leak, drip, and leak. Therefore, valve users should be treated in accordance with the situation of the user.
There are many types of valve connection. Common valve connection methods are: flange connection, butt connection, butt welding connection, thread connection, ferrule connection, clamp connection, self-sealing connection and other connection forms. This article will focus on the most common flange connection, butt welding connection and threaded connection in the installation process easy to explain the problems, I hope to help everyone.
Threaded valve: A simple connection method, often used for small valves. This connection is usually made by processing the valve inlet and outlet ends into tapered pipes or straight pipe threads, which can be connected to tapered pipe threaded joints or pipelines. Since this connection may have large leakage channels, sealants, sealing tape or fillers can be used to plug these channels. If the material of the valve body can be welded, but the expansion coefficient is very different, or the working temperature has a large range of variation, the threaded connection must be honey sealed. Threaded valves are mainly valves whose nominal diameter is below 50mm. If the diameter size is too large, the installation and sealing of the connection part will be very difficult. In order to facilitate the installation and removal of threaded valves, pipe joints can be used at appropriate positions in the pipeline system. Valves with a nominal diameter below 50mm can use pipe sockets as pipe joints, and the thread of the pipe socket connects the two connected parts together. …
Flanged valve: Flanged valve, the most used connection form among valves. Its installation and disassembly are relatively convenient. But it is heavier than the threaded valve, and the corresponding price is higher. Therefore, it is suitable for pipe connections of various diameters and pressures. However, when the temperature exceeds 350 degrees, the bolts, gaskets and flanges become loose, and the load of the bolts is significantly reduced, which may cause leakage to the flange connection with a large force.
Welded valve This connection is suitable for various pressures and temperatures, and is more reliable than flanged connections when used under heavy load conditions. However, it is difficult to disassemble and reinstall the valve connected by welding, so its use is limited to the occasions that usually can operate reliably for a long time, or where the use conditions are heavy and the temperature is high. Such as the pipelines of thermal power stations, nuclear power projects, and ethylene projects. Welded valves with a nominal diameter of less than 50mm usually have welding sockets to accept the pipeline at the end of the load. Since socket welding forms a gap between the socket and the pipe, it is possible that the gap will be corroded by some media. At the same time, the vibration of the pipe will fatigue the connection part, so the use of socket welding is limited. In the occasions where the nominal diameter is large, the use conditions are heavy, and the temperature is high, the valve body is often welded with grooves. At the same time, there are original requirements for the welding seam, and a skilled welder must be selected to complete this work.
TH Valve is a professional manufacturer of butterfly valve, gate valve, check valve, globe valve, knife gate valve, ball valve with API, JIS, DIN standard, used in Oil, Gas, Marine industry, Water supply and drainage, fire fighting, shipbuilding, water treatment and other systems, with Nominal Diameter of DN50 to DN1200, NBR/EPDM/VITON, Certificates & Approvals: DNV-GL, Lloyds, DNV, BV, API, ABS, CCS. Standards: EN 593, API609, API6D
Related news/knowledge:
Resilient seated socket end gate valve;
Commonly used valve body material code description;
The difference between internally and externally threaded valves;
Classification of check valves