Valve actuator / actuation -(4)-angle stroke valve actuator application
Angle stroke valve actuator application products:
1. Butterfly valve:
The baffle of the butterfly valve controls the flow of fluid with the rotation of the shaft. It is composed of valve body, baffle, baffle shaft and shaft seal. Its simple structure, small size, light weight, low cost and large flow capacity are especially suitable for occasions with low pressure difference, large diameter, large flow gas and fluid with su
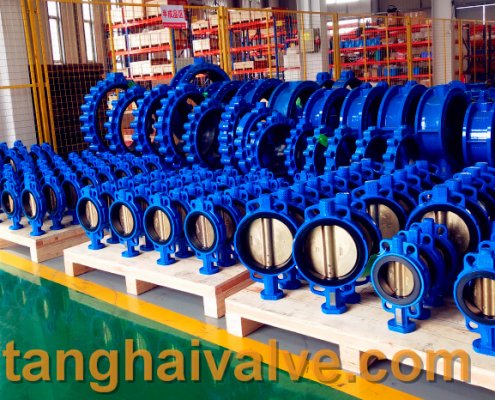
ductile iron, DI, butterfly valve, manufacturer, center line, TH valve
spended solids, but the leakage is large. Its flow characteristics are achieved at the corners. The front and equal percentage characteristics are similar, but the work will be unstable and the characteristics will not be good in the future; use in the corner range. Butterfly valves are not only widely used in general industries such as petroleum, gas, chemical, and water treatment, but also used in cooling water systems of thermal power stations.
2. Ball valve:
The ball valve is defined in the standard GB/T21465-2008 “Valve Terminology” as a valve in which the opening and
closing part (sphere) is driven by the valve stem and rotates around the axis of the valve stem. The ball valve has a 90-degree rotation. The cock body It is a sphere with a circular through hole or channel passing through its axis. It is mainly used to cut off or connect the medium in the pipeline, and can also be used for fluid adjustment and control. Among them, the hard-sealed V-shaped ball valve has a strong shear between the V-shaped core and the metal seat of the hard alloy. Shearing force is especially suitable for media containing fibers and tiny solid particles. The multi-way ball valve can not only flexibly control the confluence, divergence, and flow direction switching of the
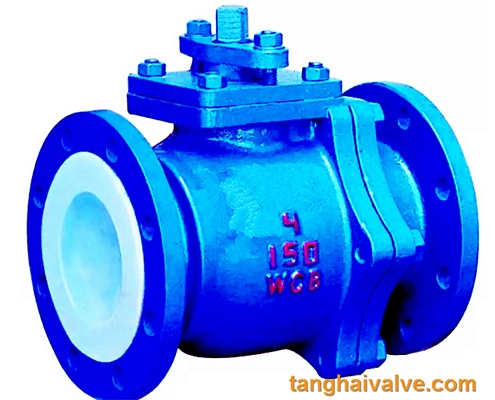
14 ball-valve-6
medium in the pipeline, but also close any channel and connect the other two channels. This type of valve should generally be installed horizontally in the pipeline. Ball valve classification: pneumatic ball valve, electric ball valve, manual ball valve. The ball valve can be closed tightly with only a 90-degree rotation and a small torque. The ball valve is most suitable for use as a switch and shut-off valve, V-shaped ball valve. In the developed western countries, the use of ball valves is increasing year by year. In our country, ball valves are widely used in petroleum refining, long-distance pipelines, chemicals, papermaking, pharmaceuticals, water conservancy, electric power, municipal administration, steel and other industries. Occupy a pivotal position in the national economy.
3. Cam flex valve:
Cam flex valve, also known as eccentric rotary valve, is also a new-type regulating valve. The center line of the spherical valve core deviates from the center of the rotating shaft, and the rotating shaft drives the valve core to rotate eccentrically, so that the valve core enters the valve seat forward and downward.
The eccentric rotary valve has the advantages of small size, light weight, reliable use, convenient maintenance, strong versatility, and low fluid resistance. It is suitable for occasions with high viscosity and has good performance in lime, mud and other fluids.
TH Valve is a professional manufacturer of butterfly valve, gate valve, check valve, globe valve, knife gate valve, ball valve with API, JIS, DIN standard, used in Oil, Gas, Marine industry, Water supply and drainage, fire fighting, shipbuilding, water treatment and other systems, with Nominal Diameter of DN50 to DN1200, NBR/EPDM/VITON, Certificates & Approvals: DNV-GL, Lloyds, DNV, BV, API, ABS, CCS. Standards: EN 593, API609, API6D
Related news/knowledge:
Types and working principles of electric valves;
Pneumatic ball valve principle, structure and working principle;
The working principle of butterfly valve (picture);
Characteristics and working principle of electric globe valve