Types of valve accessories
Types of valve accessories: The valve itself is composed of a valve body and various operating mechanisms, which also contain many parts and accessories, including manual, pneumatic, electric and so on. The components assembled in different ways of use are also different.
Valve accessories mainly include:
1. Pneumatic actuator: It is mainly divided into single-acting and double-acting. Single-acting is a spring-return
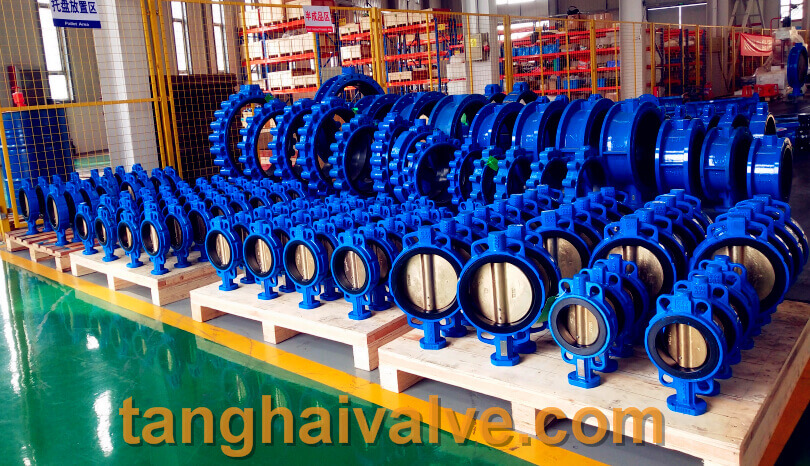
ductile iron, DI, butterfly valve, manufacturer, center line, TH valve
structure, and double-acting is the principle of air opening and closing. Generally, double-acting pneumatic actuators are used for adjustment types. 2. Electric actuators: the common ones are linear, angular, compact and explosion-proof. The structure of the electric actuator is relatively complex and the cost is high, but its performance is stable, open and close quickly, and it is suitable for remote control systems.
3. Hydraulic actuator: A hydraulic actuator is a device that converts hydraulic energy into mechanical energy. There are mainly linear and rotary types. The cost is relatively high and the structure is relatively complex. It is a product with special working conditions and high requirements, and the market generalization rate is low.
4. Gas-liquid linkage actuator: The gas-liquid linkage actuator uses pipeline natural gas or nitrogen as power and hydraulic oil as the transmission medium to drive the opening and closing of pipeline valves. It is mainly used as a multifunctional driving device in natural gas, liquefied gas, nitrogen, gas liquid tank, gas, etc.
5. Electro-hydraulic linkage actuator: The electro-hydraulic linkage actuator is composed of a control module and a power module. The intelligent controllable motor accepts the function commands of the control module, controls the power module, and outputs the large distance in line or angular displacement, pneumatic control The object, at the same time, completes the adjustment process through its own displacement feedback, and realizes various functional controls.
6. Manual actuator: The manual actuator is to perfect the manual control when the current is unstable and the air pressure is insufficient. When the air pressure and current cannot be controlled under special circumstances or there is no current and air pressure for installation and maintenance, the manual feedback device can be turned on, which can be carried out quickly Manual control.
Valve components:
Handle, handwheel, worm gear, valve body, valve core, valve stem, valve cover, valve silencer, blank, bolt and nut, clamp, spring, diaphragm, packing, packing, O-ring, PTFE products Gaskets, flanges, non-standard solid parts, etc.
Positioner and accessories:
Pneumatic valve positioner, electric valve positioner, intelligent valve positioner, electro-hydraulic server, servo amplifier, electric converter, filter pressure reducing valve, valve position transmitter, position valve, solenoid valve, limit switch, pneumatic Amplifier, smart module, electro-hydraulic server, servo amplifier, alarm, explosion-proof coil, quick exhaust valve
Other valve accessories:
Valve testing machine Handle Handwheel Worm gear valve Body Valve core Valve cover Valve silencer Signal generator Rough mold bolts and nuts Clamps Springs Diaphragm Packing O-rings Flow juice Polytetrafluoroethylene products Gaskets Flanges Fast elbows Joint expander Flow meter Filter non-standard solid parts
TH Valve is a professional manufacturer of butterfly valve, gate valve, check valve, globe valve, knife gate valve, ball valve with API, JIS, DIN standard, used in Oil, Gas, Marine industry, Water supply and drainage, fire fighting, shipbuilding, water treatment and other systems, with Nominal Diameter of DN50 to DN1200, NBR/EPDM/VITON, Certificates & Approvals: DNV-GL, Lloyds, DNV, BV, API, ABS, CCS. Standards: EN 593, API609, API6D
Related news/knowledge:
What are the accessories for pneumatic valves?
Valve accessories-bonnet bushing bolts nuts;
Uses and characteristics of manual butterfly valve (4);
The matching function and principle of pneumatic valve accessories