Instructions for the safe use of resilient seated flanged butterfly valves
The resilient seated flanged butterfly valve has the characteristics of small opening torque, flexibility and convenience, labor-saving and energy-saving. The sealing form of the soft seal has reliable performance and can achieve no leakage. Therefore, the use of flange soft-seal butterfly valve is very wide, and it has its presence in all major pipeline systems, and its safe use has gradually attracted attention.
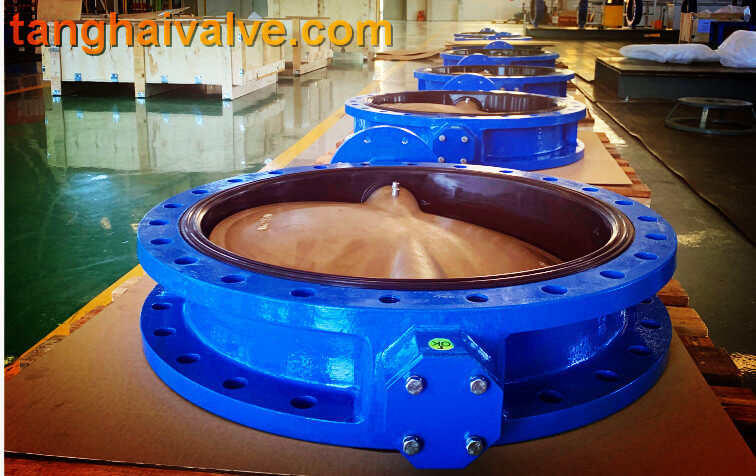
Double flange butterfly valve (16)
First of all, the safety of the valve piping system must first consider the main valve. A soft-seal flanged butterfly valve is required to be used as a safety master valve. The function is to cut off and connect the entire pipeline system. In normal production, it is also in the normally open state. The main valve is generally not used to adjust the flow rate and should be installed at the inlet of the main pipeline.
Secondly, a main valve is also needed at the inlet of the branch pipeline. The butterfly valve here is mainly used to control the branch pipeline safely. In addition to the cut-off function, the main valve of the branch pipeline also has the function of adjusting the flow rate. Adjust the flow rate to meet the needs of the branch pipeline flow size, and strictly follow a certain ratio, which is adjusted and controlled by the main valve of each branch pipeline. There should be two flanged soft-seal butterfly valves or safety valves that are often switched on or off or used for adjustment. One of the butterfly valves is spare and is normally open and not in use. A spare valve can be used if there is a problem with the working butterfly valve, so that it will not affect the production. After repairing, a butterfly valve is still reserved as a spare.
On liquid and gas pipelines, a safety drain valve is required at the lowest point or at a suitable place. The function is to empty the medium blocked in the pipeline to avoid air resistance in the pipeline. Because the gas in the pipe will reduce the pipe section, increase the transmission resistance, reduce the flow rate, and affect production. For some special liquids that will dissolve gas after a certain period of time and cannot be discharged during operation, it is also necessary to drain the butterfly valve.
The closing of the resilient seated flanged butterfly valve also has safety requirements. After the valve is closed tightly, some media will also change as the temperature changes, and the thermal expansion of the valve components will increase the pressure between the butterfly valve and the valve seat. When it is turned on again, it will inevitably bring difficulties. Therefore, the torque required to open the valve will be greater than the torque required to close the valve. The resilient seated flanged butterfly valve needs to overcome the increase of static friction due to the increase of the pressure between the sealing surfaces due to the temperature change. Because of the friction between the sealing surfaces, when the valve is closed and opened again, the required torque is much larger than the torque required to close the valve.
TH Valve is a professional manufacturer of butterfly valve, gate valve, check valve, globe valve, knife gate valve, ball valve with API, JIS, DIN standard, used in Oil, Gas, Marine industry, Water supply and drainage, fire fighting, shipbuilding, water treatment and other systems, with Nominal Diameter of DN50 to DN1200, NBR/EPDM/VITON, Certificates & Approvals: DNV-GL, Lloyds, DNV, BV, API, ABS, CCS. Standards: EN 593, API609, API6D
Video of center-lined butterfly valve: https://youtu.be/NuSZH_AJcwY
Related news/knowledge:
The role and classification of valves
Factors Affecting the Operation and Use of resilient seated butterfly valves
Introduction to the applicable occasions of butterfly valve
Applicable occasions and application conditions of butterfly valves