Valve selection basis and selection guide
How to select the righty type of valve? the following article will give you an idea how to choose the right structure/type valve.
Nowadays, there are more and more valves on the market, the types of valves are particularly complex, and the
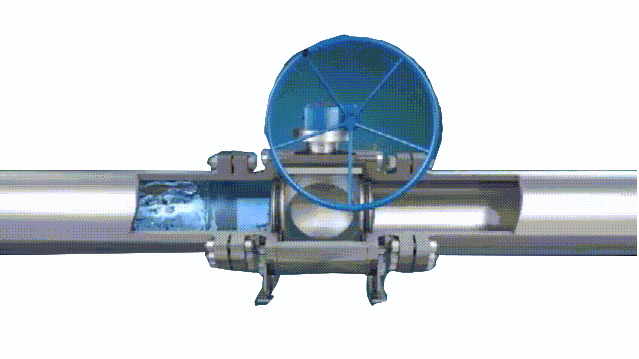
ball valve working diagram-3D GIF animated presentation
structures and materials are all different. The selection of valves is very important for the long-term operation of the device in working conditions. Improper selection of valves and users’ ignorance of valves are the source of accidents and safety threats. Nowadays, the demand for valve products in the social industry is becoming more and more extensive, and users should have a further understanding and cognition of knowledge about valves and other aspects.
There are generally two types of valve characteristics, use characteristics and structural characteristics.
Use characteristics of the valve: It determines the main use performance and use range of the valve. The
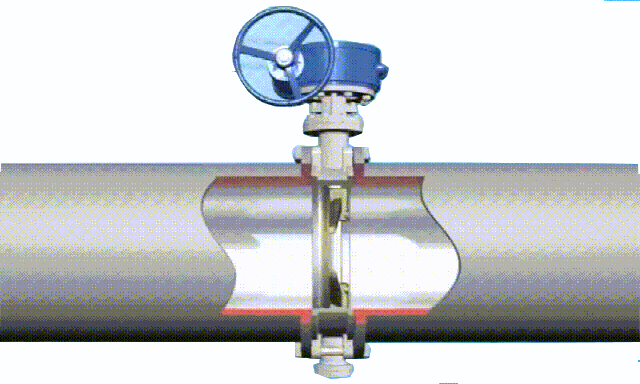
butterfly valve working diagram-3D GIF animated presentation
characteristics of the valve use include: valve category (closed circuit valve, regulating valve, safety valve, etc.); product type (gate valve, globe valve, butterfly valve, ball valve) Etc.); the materials of the main parts of the valve (valve body, bonnet, valve stem, valve disc, sealing surface); valve transmission mode, etc.
The structural characteristics of the valve: it determines the structural characteristics of the valve installation, repair, maintenance and other methods. The structural characteristics include: the structural length and overall height of the valve, the connection form with the pipeline (flange connection, threaded connection, clamp Connection, external thread connection, welding end connection, etc.); the form of the sealing surface (inlaid ring, threaded ring, surfacing, spray welding, valve body); valve stem structure (rotating rod, lifting
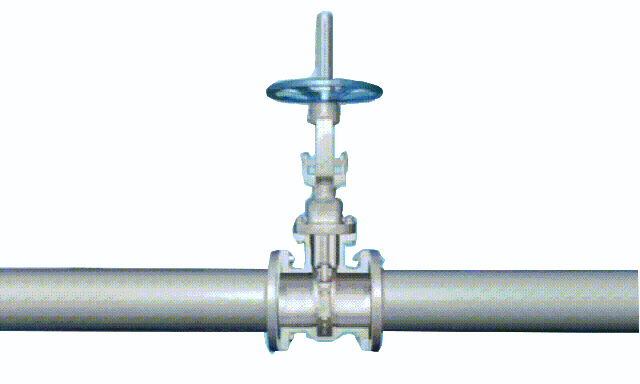
gate valve working diagram-3D GIF animated presentation
rod), etc.
Valve selection steps:
1. Clarify the purpose of the valve in the equipment or device, and determine the working conditions of the valve: applicable medium, working pressure, working temperature, etc.
2. Determine the nominal diameter and connection method of the pipe connected to the valve: flange, thread, welding, ferrule, quick installation, etc.
3. Determine the method of operating the valve: manual, electric, electromagnetic, pneumatic or hydraulic, electrical linkage or electrohydraulic linkage, etc.
4. Determine the material of the valve housing and internal parts according to the medium, working pressure and
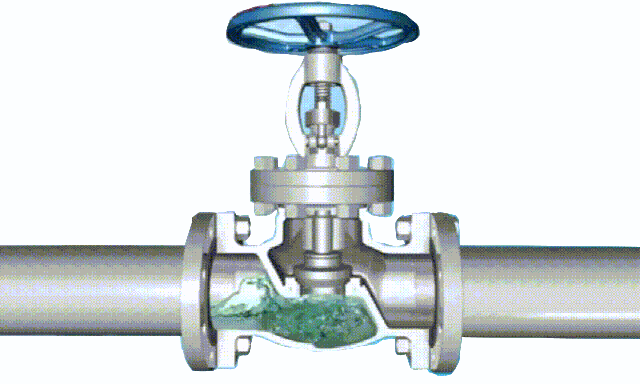
globe cut-off valve working diagram-3D GIF animated presentation
working temperature conveyed by the pipeline: gray cast iron, malleable cast iron, ductile iron, carbon steel, alloy steel, stainless acid-resistant steel, copper alloy, etc.
5 Select the type of valve: closed circuit valve, regulating valve, safety valve, etc.
6. Determine the valve type: gate valve, globe valve, ball valve, butterfly valve, throttle valve, safety valve, pressure reducing valve, steam trap, etc.
7. Determine the parameters of the valve: For automatic valves, first determine the allowable flow resistance, discharge capacity, back pressure, etc., according to different needs, and then determine the nominal diameter of the pipeline and the diameter of the valve seat hole.
8. Determine the geometric parameters of the selected valve: structural length, flange connection form and size, valve height dimension after opening and closing, connecting bolt hole size and number, overall valve outline size,
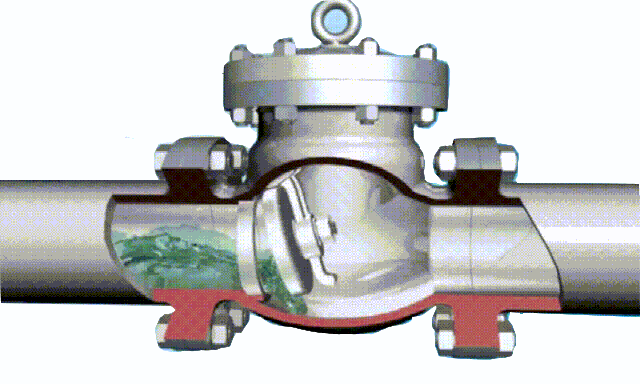
tilting disc swing check valve working diagram-3D GIF animated presentation
etc.
9. Use existing information: valve product catalog, valve product sample, etc. to select appropriate valve products.
Basis for valve selection:
1. The purpose, operating conditions and operation control mode of the selected valve.
2. The nature of the working medium: working pressure, working temperature, corrosion performance, whether it contains solid particles, whether the medium is toxic, whether it is flammable or explosive medium, the viscosity of the medium, etc.
3. Requirements for valve fluid characteristics: flow resistance, discharge capacity, flow characteristics, sealing level, etc.
4. Requirements for installation dimensions and external dimensions: nominal diameter, connection to the pipeline and connection dimensions, external dimensions or weight restrictions, etc.
5. Additional requirements for the reliability and service life of valve products and the explosion-proof performance of electric devices. (Note when selecting parameters: If the valve is to be used for control purposes, the following additional parameters must be determined: operation method, maximum and minimum flow requirements, pressure drop for normal flow, pressure drop when closed, maximum and minimum inlets of the valve Pressure.)
According to the above-mentioned basis and steps for selecting valves, the internal structure of various types of valves must be understood in detail when selecting valves reasonably and correctly, so that the correct choice can be made on the preferred valve. The ultimate control of the pipeline is the valve. The valve opening and closing parts control the flow mode of the medium in the pipeline. The shape of the valve flow channel makes the valve have a certain flow characteristic. This must be considered when selecting the most suitable valve for the pipeline system.