Generator for valve actuator:
1. The development history of generator controller The automatic control of generator set has experienced relay control. Greatly simplified the control circuit? Reliability has also been improved, to the point of more humanity,
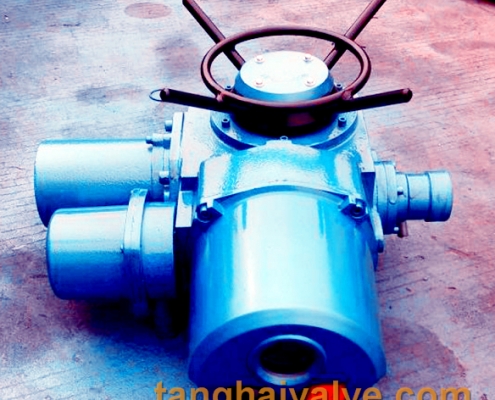
electric actuator for butterfly valve
there are also some generator manufacturers produce small gasoline engine integrated machine, practical and convenient.
2. Diesel generator set structure Diesel generator set is generally composed of three parts: engine, generator and controller. The generator powered by the engine converts the mechanical energy of the engine into electrical energy. The controller is the brain part of the generator set. It not only provides engine start-up, shutdown, data measurement, data display and fault protection functions, but also provides generator power measurement, power display and power protection functions.
3. (i.e. only provide start-up, shutdown and high water temperature, low oil pressure, overspeed protection? Does not provide power display? Water temperature meter, oil pressure meter, hour meter, battery voltmeter, AC voltmeter, AC Ammeter and other instruments), standard type (providing power display, providing protection function? Without communication interface), high-end type (in addition to providing standard functions, but also providing communication interface? Remote control, remote measurement, remote signaling functions are available, some It also has a network interface? It can be monitored through the Internet? Some have a text message function, which is more suitable for unattended computer rooms in remote areas).
Fourth, the inspection steps of the diesel generator set test machine when purchasing diesel generator sets? The customer is most concerned about the price of the generator set? There are many kinds of generator sets according to the brand? And the price of the generator set with different diesel engine power is different , Diesel generator set manufacturers will introduce to you how to compare the prices of diesel generator sets.
One question: Ask about the purchase time of the old diesel engine, ask about the repairs in the past? Which main parts have been replaced? Ask what are the problems in use? In order to have a more comprehensive and systematic understanding of the old diesel engine.
Second look: look at the signs and appearance of the old diesel engine. See which factory produced it? When did it leave the factory? How long did it take? See if the paint on the exterior is peeling off? Is there any defect? Whether the model is eliminated, etc. Judge the degree of newness of the old diesel engine from the label and appearance.
Three trials: Test machine. Check the old diesel engine carefully by shaking the crankshaft, turning the flywheel, starting the machine, etc. Test machine is a very important step? The specific inspection steps are as follows:
1. Rotate the crankshaft to supply oil from the fuel injector. If the fuel injector makes a crisp sound? It means that the performance of the fuel injector and plunger pair is still good. If there is no abnormal noise such as “whipping” in the wheel chamber, it means that the gear wear is not serious.
2. Pull up and down to fly, if there is no noise, it means that the gap between the crankshaft main shaft and the bearing bush is not large.
3. Turn the flywheel so that the piston approaches the bottom dead center? Then shake the flywheel left and right? If there is no “click” sound, it means that the wear between the connecting rod shaft and the bushing is not serious.
4. Decompress the cylinder and sway the crankshaft. When decompression is removed, if the rebound force of the piston is large, the flywheel rotates rapidly, indicating that the degree of wear of the cylinder, piston, and piston ring is small. When cranking the crankshaft, the pointer of the oil pressure gauge should be no less than 1 or the red mark of the oil instruction can rise quickly, and the hand pressure should be laborious.
5. Start the machine, if it is easy to start? The smoke is colorless or light gray? The speed is stable and no noise? It shows that the technical condition of the old diesel engine is good. Remarks: During the testing process of diesel generator set, it is best to operate and track changes in data such as air pressure and oil pressure in the diesel generator controller. Therefore, the stability of the quality of the diesel generator controller has high requirements in terms of humanization and other aspects. This controller is highly evaluated in the market.
6. How to buy diesel generator sets What issues should companies pay attention to when purchasing diesel generator sets? Diesel generator sets are widely used in telecommunications, financial and financial departments, hospitals, schools, commerce and other departments, industrial and mining enterprises and other special purpose independent power supply. Enterprises must have their own standards when purchasing diesel generator sets.
1. The performance and quality of the diesel generator set to be purchased must meet the requirements of relevant standards. The diesel generator set for communication must meet the requirements of the G3 or G4 level in GB2820-1997? At the same time as the “Communication diesel generator set into the network The 24 performance index requirements stipulated in the Implementation Rules for Quality Certification and Testing? At the same time, it must pass the strict inspection of the Communication Power Equipment Quality Supervision and Inspection Center established by the Chinese industry authority. The purchase of diesel generator sets for military communications must meet the relevant GB2820-1997, GJB related standards and the provisions of the “Quality Inspection Standards for Communication Power Equipment” formulated by relevant military departments, and must pass the strict inspection of the equipment quality by the organization department.
2. The main factors that should be considered when purchasing diesel generator sets. The main factors that should be considered when purchasing diesel generator sets are mechanical and electrical performance, the purpose of the unit, the capacity and range of load changes, and automation functions.
1. The purpose of diesel generator set. Because diesel generator sets can be used in three situations: common use, standby and emergency. Therefore, different applications have different requirements for diesel generator sets.
2. Load capacity of diesel generator set. The load capacity and load variation range should be selected according to different uses. Determine the single engine capacity of the diesel generator set and the capacity of the standby diesel generator set.
3. Environmental conditions for the use of diesel generator sets. Mainly refers to altitude and climatic conditions.
4. Selection of diesel generator set
5. Pay attention to generator and excitation mode when purchasing diesel generator set
6. Selection of the automation function of diesel generator set
TH Valve is a professional manufacturer of butterfly valve, gate valve, check valve, globe valve, knife gate valve, ball valve with API, JIS, DIN standard, used in Oil, Gas, Marine industry, Water supply and drainage, fire fighting, shipbuilding, water treatment and other systems, with Nominal Diameter of DN50 to DN1200, NBR/EPDM/VITON, Certificates & Approvals: DNV-GL, Lloyds, DNV, BV, API, ABS, CCS. Standards: EN 593, API609, API6D
Related news/knowledge:
Valve actuator / actuation -(6)-Control panel;
Valve actuator / actuation -(2)-classification and working principle;
What is machining accuracy, machining error, tolerance?
Installation requirements for manual butterfly valves