Commonly Used Seat Materials for Butterfly Valve
The valve seat is a detachable part inside the valve. Its main function is to support the valve core to be fully closed or fully closed, and to form a sealing pair. Under normal circumstances, the diameter of the valve seat is the size of the valve. The butterfly valve seat is made of a wide range of materials, but the commonly used materials include soft-seal EPDM, nitrile rubber (NBR), polytetrafluoroethylene (PTFE), and metal hard-seal hard alloy materials. kind. Let’s introduce them one by one below.
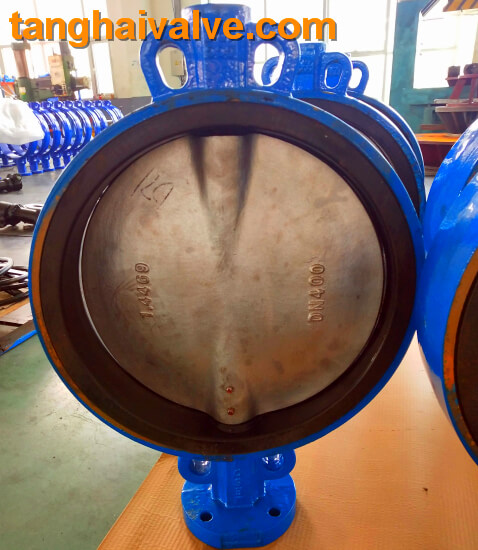
wafer type butterfly valve, EPDM seat (10)
1. EPDM: Compared with other general-purpose rubbers, EPDM has great advantages.
①The cost performance is very high. Among the commonly used rubbers, EPDM has the lightest raw rubber density and can be filled in a large amount, reducing the cost of the rubber.
②EPDM material is resistant to aging, sun exposure, heat resistance, moisture resistance, and radiation resistance, and is suitable for weak acid and weak alkali media. Good insulation properties.
③The applicable temperature range can be as low as -40℃–60℃, and it can be used for a long time under the temperature condition of 130℃.
2. Nitrile rubber (NBR): oil resistance, heat resistance, abrasion resistance and good water resistance, air tightness and excellent bonding properties. It is widely used in petroleum pipelines. The disadvantage is that it is not resistant to low temperature, ozone, poor insulation performance, and general elasticity.
3. Polytetrafluoroethylene (PTFE): A fluoroplastic, this material has strong resistance to acids, alkalis, and various organic solvents. At the same time, the material is resistant to high temperatures and can be used continuously at 260°C, and the maximum use temperature can reach 290-320°C. The emergence of PTFE has successfully solved many problems in the chemical, petroleum, pharmaceutical and other industries.
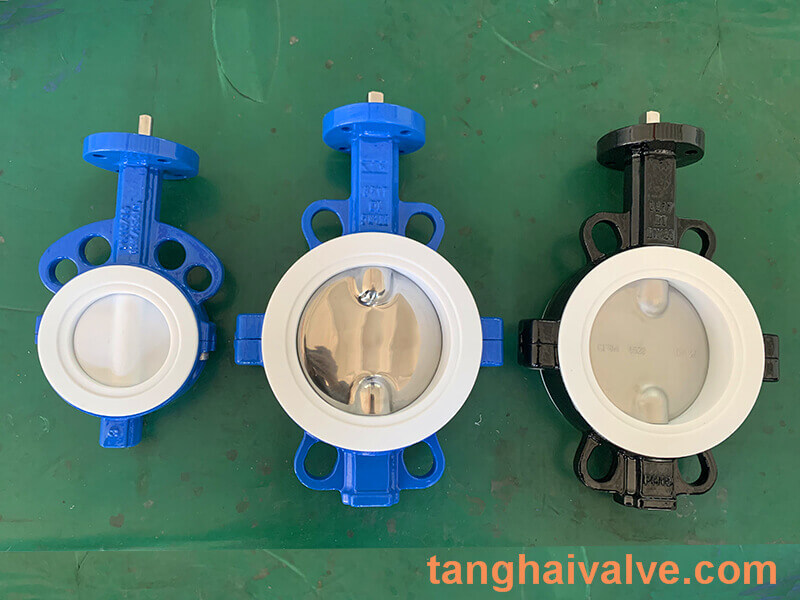
Fluorine lined butterfly valve-PTFE-WAFER (8)
4. Metal hard seal (hard alloy): The material of the metal hard seal valve seat has very good high temperature and high pressure resistance, corrosion resistance, wear resistance and other characteristics, which makes up for the defects of soft seal material that is not resistant to high temperature and high pressure. However, the hard seal material has high requirements on the processing technology. The only disadvantage of the metal hard seal valve seat is that the sealing performance is poor, and leakage will occur after a long time of operation.
TH Valve is a professional manufacturer of butterfly valve, gate valve, check valve, globe valve, knife gate valve, ball valve with API, JIS, DIN standard, used in Oil, Gas, Marine industry, Water supply and drainage, fire fighting, shipbuilding, water treatment and other systems, with Nominal Diameter of DN50 to DN1200, NBR/EPDM/VITON, Certificates & Approvals: DNV-GL, Lloyds, DNV, BV, API, ABS, CCS. Standards: EN 593, API609, API6D
Related news/knowledge:
Valve seat sealing (TH-VSE)
What is the difference between lining and vulcanized valve seat?
What is the material of the main parts of the butterfly valve?-(2)
The chemical composition, characteristics and applications of rubbers