What is butt welding? (3)- flash butt welding
Flash butt welding
Flash butt welding can be divided into continuous flash butt welding and preheated flash butt welding. Continuous flash butt welding consists of two main stages: the flash stage and the upsetting stage. Preheating flash butt welding only adds a preheating stage before the flashing stage.
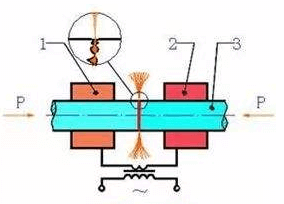
flash butt welding-schematic diagram
One, two stages of flash butt welding
1, flash stage
The main function of flash is to heat the workpiece. In this stage, the power is turned on first, and the end faces of the two workpieces are slightly contacted, forming many contact points. When the current passes, the contact points melt and become liquid metal lintels connecting the two ends. Due to the extremely high current density in the liquid lintel, the liquid metal in the lintel evaporates and the lintel blasts. With the slow advancement of the movable clamp, the lintels are also continuously produced and blasted. Under the action of vapor pressure and electromagnetic force, liquid metal particles are continuously ejected from the interface. The formation of a rapid stream of sparks-flash.
In the flashing process, the workpiece gradually shortens and the temperature of the tip gradually rises. As the end temperature increases, the blasting speed of the lintel will increase, and the advancing speed of the movable clamp must be gradually increased. Before the flashing process ends, a layer of liquid metal must be formed on the entire end surface of the workpiece, and the metal must reach the plastic deformation temperature at a certain depth.
Due to the strong oxidation of metal vapor and metal particles generated during lintel blasting, the oxygen content of the gas medium in the interface gap is reduced, and its oxidation capacity can be reduced, thereby improving the quality of the joint. But the flash must be stable and strong. The so-called stability means that no open circuit or short circuit occurs during the flashing process. The open circuit will weaken the self-protection effect of the weld, and the joint will be easily oxidized. A short circuit will overburn the workpiece and cause the workpiece to be scrapped. The so-called strong means that there are quite a lot of lintel blasts per unit time. The stronger the flash, the better the self-protection of the weld, which is especially important in the later flash.
2, upsetting stage
At the end of the flashing stage, immediately apply sufficient top pressure to the workpiece, and the interface gap is rapidly reduced, and the lintel stops blasting, that is, the upsetting stage is entered. The function of upsetting is to seal the gap between the end face of the workpiece and the fire hole left by the liquid metal lintel after blasting, while extruding the liquid metal and oxide inclusions on the end face, so that the clean plastic metal is in close contact, and the joint area produces a certain degree of plasticity Deformation to promote the progress of recrystallization, form common crystal grains, and obtain a strong joint. Although there is molten metal during the heating process in flash butt welding, it is actually welding in a plastic state.
Preheating flash butt welding is to heat the workpiece with intermittent current pulses before the flash phase, and then enter the flash and upsetting phase. The purpose of preheating is as follows:
(1) Reduce the required power to weld workpieces with larger cross-sectional area on a small capacity welder, because when the capacity of the welder is insufficient, it is impossible to stimulate continuous flashing without preheating the workpiece to a certain temperature. process. At this time, preheating is a last resort.
(2) Reduce the cooling rate after welding. This will help prevent the quenched structure and cracks of the quenched steel joint during cooling.
(3) Shortening the flash time can reduce the flash margin and save precious metals.
The shortcomings of preheating are:
(1) Extend the welding cycle and reduce the productivity;
(2) Make the process automation more complicated;
(3) Preheating control is difficult. If the preheating degree is inconsistent, the stability of the joint quality will be reduced.
TH Valve is a professional manufacturer of butterfly valve, gate valve, check valve, globe valve, knife gate valve, ball valve with API, JIS, DIN standard, used in Oil, Gas, Marine industry, Water supply and drainage, fire fighting, shipbuilding, water treatment and other systems, with Nominal Diameter of DN50 to DN1200, NBR/EPDM/VITON, Certificates & Approvals: DNV-GL, Lloyds, DNV, BV, API, ABS, CCS. Standards: EN 593, API609, API6D
Related news/knowledge:
What is butt welding? (5)- flash butt welding;
What is butt welding? (4)- flash butt welding;
What is butt welding? (7)- Flash butt welding of common metals;
What is butt welding? (1)