factors affecting the sealing performance of resilient butterfly valve seat
Rubber butterfly valve is an important part of regulating flow medium, and tight sealing is the most important quality of the product. The sealing performance of rubber butterfly valves is affected by many factors, and the most important influence is still closely related to the sealing surface. Today we will focus on three factors. Let’s take a
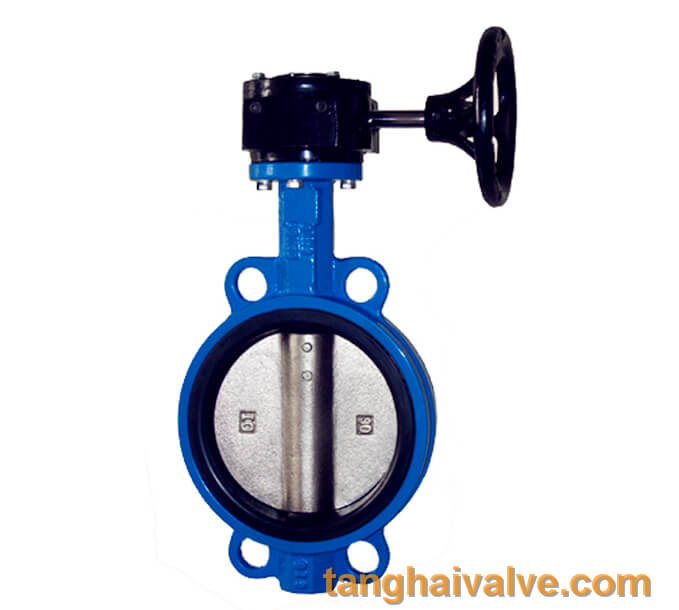
Wafer type butterfly valve with worm gear
look at the main factors that affect the sealing performance of rubber butterfly valves:
1. Quality of the sealing surface/valve seat
First of all, we must make it clear that the sealing surface refers to the part where the valve seat and the disc are in contact with each other for medium opening and closing control, and only which part of the valve seat and the disc are in contact instead of the entire sealing pair. The quality of the sealing surface is mainly related to the quality of the sealing material. The quality of the sealing material should be produced by the brand manufacturer and qualified in process. In addition, the choice of sealing material should be in line with the medium. For example, rubber butterfly valves cannot be used for highly corrosive media.
2. Width of sealing surface/valve seat
The width of the sealing surface mainly affects the movement resistance of the fluid. The larger the sealing surface, the lower the resistance, and the narrower the resistance is relatively large. Therefore, the increase in the width of the sealing surface can reduce the erosion and wear of the sealing surface by the fluid. At the same time, because the increase in the width of the sealing surface increases the length of the leakage stroke proportionally, the leakage can be reduced proportionally. However, the width of the sealing surface must not be excessively increased, because an increase in the width of the sealing surface, under the same sealing force, the reduction of the specific pressure of the seal will increase the possibility of leakage.
3. The pressure difference between before and after the valve
The specific pressure on the sealing surface is caused by the pressure difference between the front and rear of the valve and the applied sealing force, which refers to the pressure acting on a unit area of the sealing surface. The specific pressure directly affects the sealing performance, reliability and service life of the rubber butterfly valve. When the specific pressure on the sealing surface is small and the surface roughness is low, the leakage increases rapidly. When the specific pressure on the sealing surface is large, the effect of surface roughness on the leakage is significantly reduced.
In addition, the sealing performance of the rubber butterfly valve is related to the sealing surface material of the butterfly valve and its processing state, the nature of the medium, the existence of the sealing oil film, the rigidity and structural characteristics of the closing part, and so on. For more information, please call Tanghai for inquiries, and we will have professionals to answer your questions about butterfly valves.
TH Valve is a professional manufacturer of butterfly valve, gate valve, check valve, globe valve, knife gate valve, ball valve with API, JIS, DIN standard, used in Oil, Gas, Marine industry, Water supply and drainage, fire fighting, shipbuilding, water treatment and other systems, with Nominal Diameter of DN50 to DN1200, NBR/EPDM/VITON, Certificates & Approvals: DNV-GL, Lloyds, DNV, BV, API, ABS, CCS. Standards: EN 593, API609, API6D
Related news/knowledge:
Factors Affecting the Operation and Use of resilient seated Butterfly Valves
What are the main factors affecting valve sealing?
Installation requirements for manual butterfly valves