Troubleshoot reasons for pneumatic wafer butterfly valves
The pneumatic wafer butterfly valve has a beautiful appearance and is matched with a pneumatic actuator. The valve plate and the valve shaft can be connected without a pin, and the medium is completely isolated from the valve shaft and valve body, which is simple and easy to maintain. Pneumatic wafer butterfly valves are widely used in industrial automation systems in food, environmental protection, light industry, petroleum, papermaking, chemical, electric power and other industries. Pneumatic wafer butterfly valves are divided into soft seal and hard seal, and the two products also have their own different characteristics.
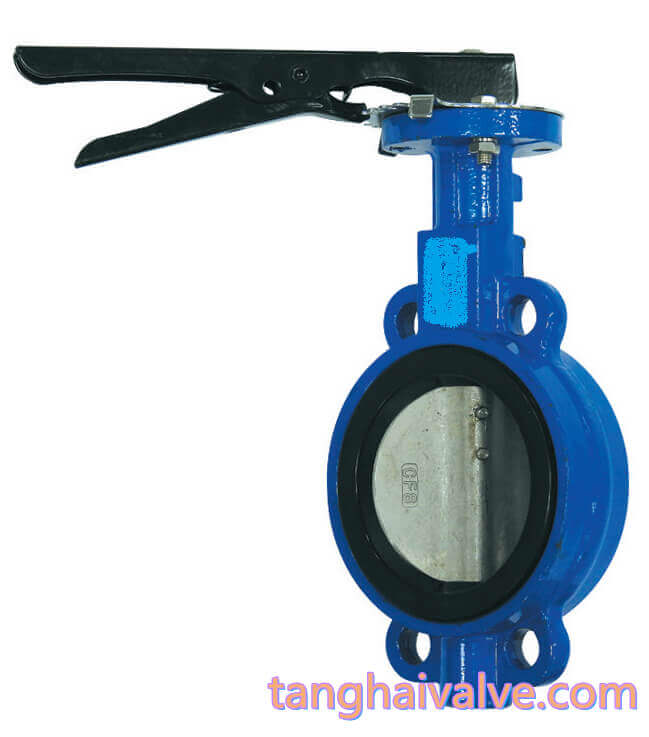
JIS 10K-wafer butterfly valve-backup seat (1)
The design features of the high-quality pneumatic wafer butterfly valve include: the valve body and end cover adopt dewaxing precision casting; the valve stem has an explosion-proof design; the standard air source interface can be directly connected to the solenoid valve; the cylinder inner wall anode hardening does not require secondary lubrication ; Switch position +/-5° stroke adjustment, easy to operate; 360°C any angle installation, etc. Its performance specifications are: nominal pressure: 1.0MPa-2.5MPa, nominal passage: DN32~DN600, applicable temperature: -20~+120 ℃. The hard seal will be higher. The soft-seal pneumatic wafer butterfly valve is used in normal temperature environment. The hard-sealed and soft-sealed pneumatic wafer butterfly valve can be used in low temperature, normal temperature, high temperature and other environments.
In use, we sometimes encounter the phenomenon that the pneumatic wafer butterfly valve does not work. Is it improper use or product quality? How do we troubleshoot the cause? Here is a reference. Pneumatic wafer butterfly valves are mainly composed of pneumatic actuators and butterfly valves. Pneumatic accessories are installed according to user requirements. Pneumatic accessories for on-off type pneumatic butterfly valves include solenoid valves and limit switches, adjustable type with positioners and filter decompression Device. Therefore, when the pneumatic wafer butterfly valve fails, it is necessary to investigate the cause one by one from each component.
The main points are as follows:
1. Pneumatic actuator:
(1) There is no air source and the air source is not opened (2) The air source pressure is insufficient (3) The cylinder piston is aging and fractured (4) The rack of the piston gear is worn (5) The single-acting actuator is rusted due to the long-term use of the spring;
2. Valve body:
(1) The valve stem is twisted or broken (2) The valve stem is rusted due to internal leakage of the medium (3) The medium has impurities and the valve plate and valve seat are stuck
3. Solenoid valve:
(1) If the terminal is loose or falling off, no electricity (2) The coil is burnt out (3) The solenoid valve is easy to get stuck when there are impurities or too little lubricating oil (4) Air leakage, the solenoid valve leaks and the air source pressure is insufficient;
4. Positioner:
(1) The air source is not turned on (2) In winter, the air source contains water and freezes causing the air duct and filter to be blocked (3) The regulator fails and the regulating mesh diaphragm is damaged;
TH Valve is a professional manufacturer of butterfly valve, gate valve, check valve, globe valve, knife gate valve, ball valve with API, JIS, DIN standard, used in Oil, Gas, Marine industry, Water supply and drainage, fire fighting, shipbuilding, water treatment and other systems, with Nominal Diameter of DN50 to DN1200, NBR/EPDM/VITON, Certificates & Approvals: DNV-GL, Lloyds, DNV, BV, API, ABS, CCS. Standards: EN 593, API609, API6D
Video of center-lined butterfly valve:
Related news/knowledge:
Troubleshooting of check valve
What are the accessories for pneumatic valves?
Working Principle of Pneumatic Gate Valve
The difference and selection of electric valve and pneumatic valve